Cutting-edge technology in plastic extrusion for current industries
Cutting-edge technology in plastic extrusion for current industries
Blog Article
A Comprehensive Overview to the Refine and Advantages of Plastic Extrusion
In the substantial realm of manufacturing, plastic extrusion arises as a necessary and highly effective procedure. Translating raw plastic into continual accounts, it caters to a myriad of markets with its impressive flexibility.
Comprehending the Basics of Plastic Extrusion
While it may appear complex at first look, the process of plastic extrusion is essentially simple. The process starts with the feeding of plastic product, in the kind of powders, pellets, or granules, into a warmed barrel. The shaped plastic is after that cooled, strengthened, and cut into wanted lengths, finishing the process.
The Technical Process of Plastic Extrusion Explained
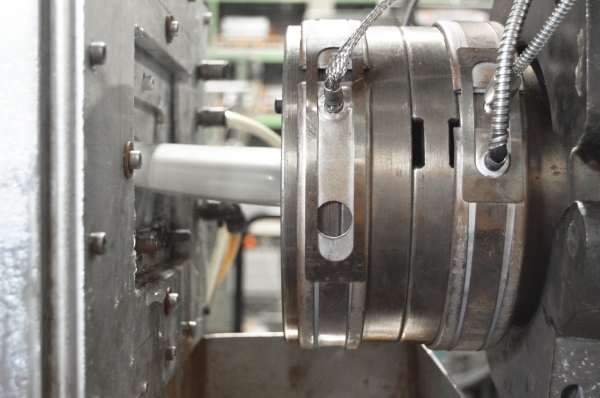
Types of Plastic Suitable for Extrusion
The option of the appropriate type of plastic is a vital facet of the extrusion procedure. Different plastics supply unique residential or commercial properties, making them a lot more fit to particular applications. Polyethylene, for example, is typically used because of its reduced price and very easy formability. It provides exceptional resistance to chemicals and wetness, making it suitable for products like tubes and containers. In a similar way, polypropylene is an additional prominent option as a result of its high melting point and resistance to tiredness. For even more durable applications, polystyrene and PVC (polyvinyl chloride) are usually picked for their strength and toughness. These are usual alternatives, the option eventually depends on the particular requirements of the item being created. So, comprehending these plastic types can considerably enhance the extrusion procedure.
Contrasting Plastic Extrusion to Other Plastic Forming Methods
Recognizing the kinds of plastic suitable for extrusion paves the means for a more comprehensive discussion on how plastic extrusion stacks up against other plastic developing approaches. Plastic extrusion is exceptional when it comes to producing continual accounts, such as gaskets, seals, and pipes. It also allows for a constant cross-section along the size of the item.
Trick Benefits of Plastic Extrusion in Manufacturing
In the world of manufacturing, plastic extrusion uses lots of substantial benefits. One notable advantage is the cost-effectiveness of the procedure, that makes it a financially attractive production method. Additionally, this strategy gives premium item adaptability and boosted production speed, consequently boosting general manufacturing effectiveness.
Cost-efficient Manufacturing Technique
Plastic extrusion leaps to the forefront as a cost-effective manufacturing approach in production. This process attracts attention for its capability to create high quantities of hop over to here product swiftly and effectively, giving producers with substantial cost savings. The primary cost benefit is the ability to make use of less pricey basic materials. Extrusion uses thermoplastic products, which are much less expensive contrasted to metals or ceramics. Additionally, the extrusion process itself is relatively simple, lowering labor costs. Furthermore, plastic extrusion requires much less power than traditional manufacturing approaches, contributing to reduced functional costs. The process additionally reduces waste, as any type of defective or excess materials can be recycled and recycled, offering an additional layer of cost-effectiveness. In general, the monetary advantages make plastic extrusion a highly eye-catching alternative in the manufacturing industry.
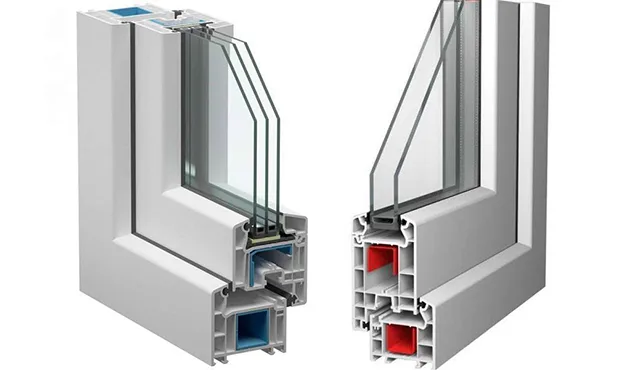
Superior Product Flexibility
Beyond the cost-effectiveness of plastic extrusion, an additional substantial advantage in manufacturing depend on its remarkable product adaptability. This process enables for the development of a large variety of items with differing layouts, sizes, and shapes, from basic plastic sheets to complex accounts. The adaptability is associated to the extrusion die, which can be tailored to produce the wanted item style. This makes plastic extrusion a suitable service for sectors that call for personalized plastic parts, such as auto, construction, and product packaging. The ability to generate diverse products is not just useful in conference certain market needs yet likewise in enabling makers to explore new line of product with minimal capital expense. In essence, plastic extrusion's product adaptability promotes advancement while improving operational efficiency.
Enhanced Production Speed
A considerable advantage of plastic extrusion depends on its enhanced manufacturing speed. This manufacturing procedure permits high-volume manufacturing in a reasonably short time span. It is capable of generating long, constant plastic accounts, which substantially lowers the manufacturing time. This high-speed production is specifically advantageous in industries where big amounts of plastic components are required within limited deadlines. Few various other production processes can match the speed of plastic extrusion. Additionally, the capacity to keep consistent high-speed production without compromising product top quality establishes plastic extrusion read here in addition to various other methods. The enhanced manufacturing rate, for that reason, not just makes it possible for suppliers to fulfill high-demand orders however additionally contributes to increased performance and cost-effectiveness. This useful attribute Read More Here of plastic extrusion has actually made it a recommended option in many markets.
Real-world Applications and Effects of Plastic Extrusion
In the world of manufacturing, the strategy of plastic extrusion holds extensive importance. The economic benefit of plastic extrusion, mainly its high-volume and cost-efficient output, has transformed production. The market is constantly aiming for innovations in eco-friendly and recyclable products, showing a future where the advantages of plastic extrusion can be retained without compromising environmental sustainability.
Conclusion
To conclude, plastic extrusion is a efficient and extremely efficient method of transforming basic materials right into varied products. It provides various advantages over various other plastic forming methods, consisting of cost-effectiveness, high result, very little waste, and layout adaptability. Its effect is exceptionally felt in different markets such as building, automobile, and customer items, making it a critical process in today's production landscape.
Digging deeper into the technological process of plastic extrusion, it starts with the choice of the ideal plastic material. Once cooled, the plastic is cut right into the needed lengths or injury onto reels if the product is a plastic movie or sheet - plastic extrusion. Contrasting Plastic Extrusion to Other Plastic Forming Approaches
Recognizing the kinds of plastic ideal for extrusion paves the means for a wider discussion on how plastic extrusion piles up against various other plastic developing techniques. Few various other manufacturing procedures can match the speed of plastic extrusion.
Report this page